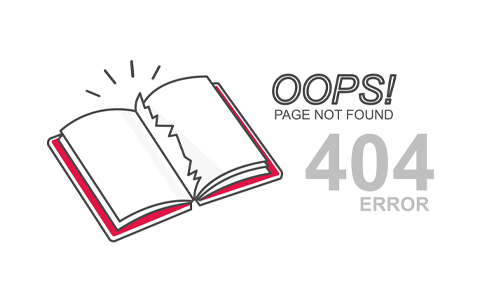
Sorry we couldn’t find what you are looking for or the page no longer exist
Perhaps you can return to the homepage and see if you can find what you are looking for. Or, you can click on the product selector icons below
The a.b.e.® range of products falls into the following broad categories: