Two-Component structural repair epoxy mortar
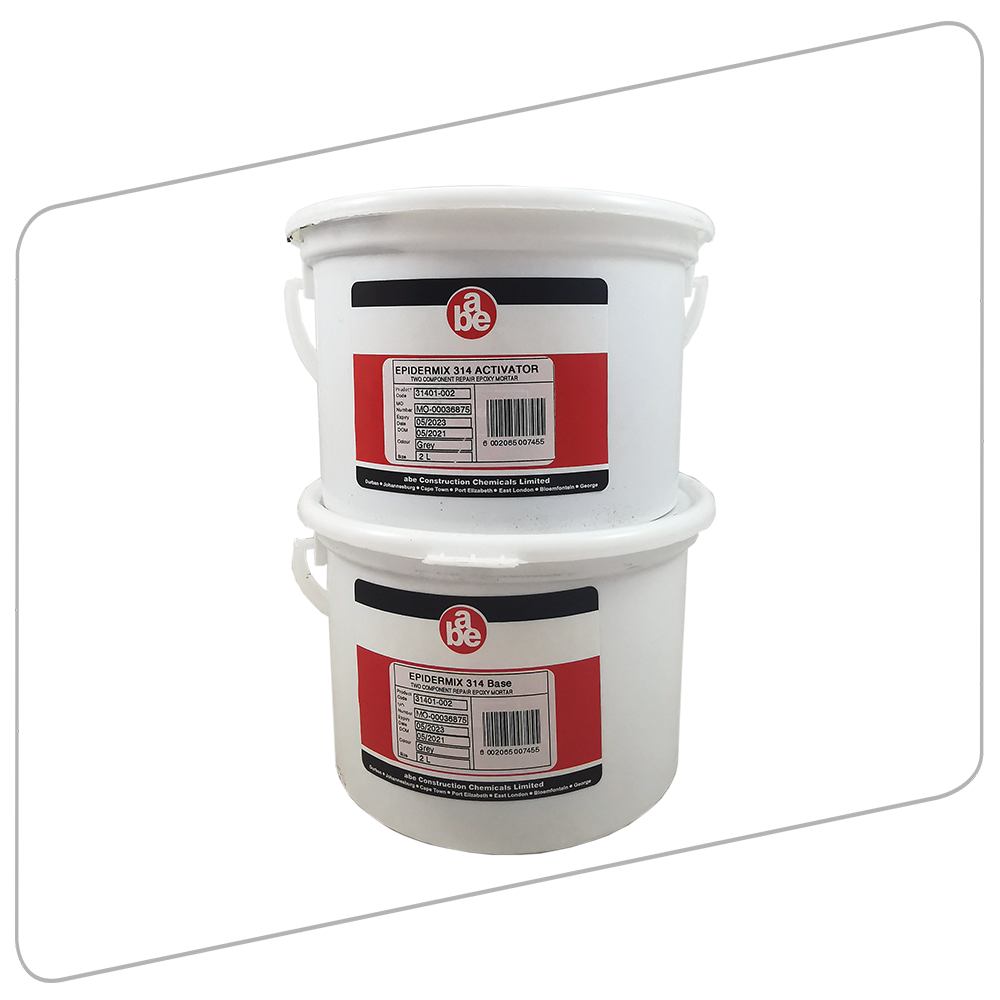
Two-component, solvent-free, filled, polyamide cured epoxy.
Uses:
Repairing and patching defects in concrete such as honeycomb and spalls.
Advantages
- Easily installed by gloved hand
- Easily smoothed to finish off
- Holds perfectly in overhead work
- Non-slump in vertical
- Needs no priming
- Strengths way above surrounding concrete
- Resistant to oils, fuels, water, dilute chemicals
- Non toxic in water containment
Surface Preparation
Any surface to be repaired with epidermix® 314 must be clean, mechanically sound and dry. The surface should be chipped to expose main aggregate and in the case of honeycomb, all suspect material must be cut out. The surface must be free of all debris prior to placing the compound.
Bonding / Priming
Self priming.
Properties of Wet Material
Mixing ratio | 1 : 1 by volume |
Density (typical) | 1.91 g/cm3 |
Colour | Base: Off white Activator: Grey Mixed: Grey – similar to concrete |
Finish | Trowelled to smooth finish with water – wet steel trowel |
Flash point | 150 ºC |
Dilution | Do not dilute |
Consistency | Each component is a heavy paste |
Toxicity | Uncured material is toxic |
Properties During Application
Application by | Gloved hand and/or steel trowel |
Pot life @ 25 ºC | 110 – 130 minutes/500ml |
Volume solids | 100% |
Theoretical coverage | 1 m2/l/1 mm thickness |
Wet thickness at above | 1 mm |
Maximum recommended thickness per layer | 25 mm |
Curing time @ 25 ºC | Touch dry 6 hrs Practical cure 12 hrs |
Overcoating time @ 25 ºC | Minimum – 8 hrs Maximum – 24 hrs |
Applicaton temp. Range | 10 ºC to 40 ºC |
Fire resistance of wet material | Non-flammable |
Equipment clean-up | a.b.e.® super brush cleaner |
Properties of Cured Material
Maximum service temperature | Dry – 70ºC Wet – 60 ºC |
Compressive strength @ 25 ºC | 60 MPa in 24 hrs 74 MPa in 7 days |
Tensile strength @ 25 ºC | 8 MPa |
Lap shear on grit blasted steel | 2 mm bondline thickness |
Arizone shear test | Concrete failure in bondline at 400 kN load 44 MPa concrete |
Shrinkage during cure | Negligible |
Toxicity | Non-toxic |
Water resistance | Excellent |
Tainting | Will not taint water |
Solvent resistance | Resists aliphatic solvents, oils, petrol, diesel, fuel |
Chemical resistance | Resists dilute inorganic acids and dilute alkalis |
Mixing
epidermix® 314 is a heavy paste to the extent that it can only be mixed by kneading with gloved hands. Set up equal volumes of base and activator side by side on a clean board. Do not take more than about 250ml of each compound at one time. Knead the two components together (like mixing bread dough) for at least five minutes.
The mixing surface and gloves should be wetted with clean water.
Coverage
1 m2/ℓ/1 mm thick.
Application
Mixed epidermix® 314 should be pressed into place in the repair area, always using a gloved hand. The viscosity of epidermix® 314 is sufficient to hold its place in soffit repairs and on vertical faces. If the void is too big to fill in one placing, leave the contact surface rough to act as a key for subsequent placing once the first application has set. A final smooth finish may be obtained by trowelling off the surface of the still uncured epidermix® 314 with a water-dampened steel trowel.
Cleaning
abe® super brush cleaner before dried/cured.
Protection on Completion
Against traffic and spillage until cured. Most epoxies chalk and degrade in extensive sunlight.
Temperature & Relative Humidity
See “Properties of Materials, Properties During Application, Cured and Wet”.
Model Specification
This product has a shelf life of 12 months if kept in a dry cool place in the original packaging. In more extreme conditions this period might be shortened.
Store in dry conditions in the original containers. If stored at high temperatures and/or high humidity conditions the shelf life may be reduced.
durarep® ZR primer is fl ammable. Keep away from sources of ignition. No smoking. In the event of fire, extinguish with CO² for foam. Do not use a
water jet.
Health & Safety
The mortar shall be epidermix® 314 , a two component, solvent free, polyamide cured epoxy mortar applied in accordance with the manufacturers recommendations, a.b.e.®. The cured mortar shall have a compressive strength of 74 MPa in seven days and be resistant to aliphatic solvents, oils, petrol and diesel fuel.
Packaging
epidermix® 314 is supplied in 2 ℓ and 4 ℓ kits.
Handling & Storage
This product has a shelf life of 24 months if kept in a dry cool place in the original packaging. In more extreme conditions this period might be shortened.
Health & Safety
Uncured epidermix® 314 is toxic and flammable. Always ventilate the working area well during application and drying. Avoid flames in vicinity. Always wear gloves when working with the material and avoid excessive inhalation and skin contact. If material is splashed in the eye, wash with copious quantities of clean water and seek medical attention.
Cured epidermix® 314 is inert and harmless. When transporting liquids and semi liquids by aircraft, ask for material safety data sheet.
Important Note
This data sheet is issued as a guide to the use of the product(s) concerned. Whilst a.b.e.® endeavours to ensure that any advice, recommendation, specification or information is accurate and correct, the company cannot accept any liability for application – because a.b.e.® has no direct or continuous control over where and how a.b.e.® products are applied.
Further Information
Where other products are to be used in conjunction with this material, the relevant technical data sheets should be consulted to determine total
requirements.
a.b.e.® has a wealth of technical and practical experience built up over the years in the company’s pursuit of excellence in building and construction
technology.
Please consult our website for our latest datasheets.